The measured stress is analyzed in a distributed way inside the sensors. The analysis methods are used to identify the static, dynamic, and slow-changing, temperature components from the signal and calculate different signal characteristics.
The results are transmitted to the central unit, normally on the bridge, to be further analyzed, data logged, and displayed to the bridge personnel to assist the navigation. The various components of a typical hull stress monitoring system are described as, strain sensors, accelerometer units, bow pressure transducers, and the bridge display unit
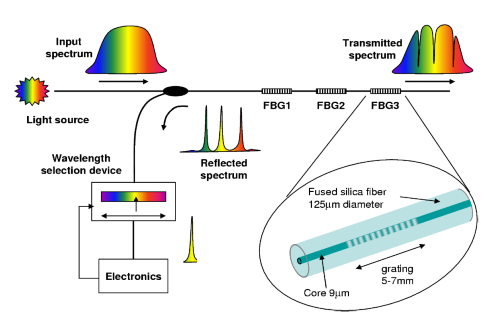
SENSFIB Hull™ Stress Monitoring Systems is based on Fiber Bragg grating
SENSFIB Hull™ Stress Monitoring Systems is based on Fiber Bragg Grating (FBG) sensors. The FBGs are an internal stripe pattern in the core of the optical fiber that strongly reflects one wavelength (or color) of light & the user interface can be configured to show current stress, fatigue accumulation, accelerations, and slamming trends as well as sailing conditions in terms of sea state, wind, speed and position if such equipment is integrated.
The Fiber Bragg Grating (FBG) optical sensing technology gives SENSFIB™ a competitive edge compared to the conventional Strain Gauge based sensors. Their key advantages are:
- Sensors are intrinsically safe requiring no ZB and no limitation to their positioning.
- Reliable as they are immune to EMI. & the software is based on a Linux OS platform.
- Accurate as the stress measurements are based on measurement of the wavelength of light.
- Reduced ownerships costs. (Recalibration, maintenance, repairs and service)
- Flexibility due to ease of installation (no hot works required for sensor installation) and
- The basic HSM system can be easily expanded to include fatigue monitoring in the water line, bow sensors for ice load monitoring etc., as desired.
Helps the navigators to monitor the current status on hull stress
Safe and cost-effective operation of a vessel requires exact knowledge of the ship's design and awareness of the operational risks and their consequences. Bulk/LNG Carriers, Tankers, and Container Vessels are particularly at risk of hull fatigue damage, induced by the stresses that can occur in the hull as a result of ballast, cargo load, and sea state. Fatigue build-up in vessels leads to local cracks in the hull, which, if left unrepaired, eventually endanger the vessel's structural integrity.
The hull stress is one of the major factors which cause irretraceable damage to merchant marines. Fatigue accumulated in vessels leads to local cracks in the hull, which are subjected to catastrophic structural failure. Then, this might call a very dangerous situation - with the consequent loss of life. One of the challenges involved has been the lack of information on the bridge about the actual load on the hull/structure. To reduce this type of damage, a tool is required which can collect this type of information and make it easily available at the bridge for the navigator. To reduce the incidence of such failures, IMO and leading Classification Societies have recommended the use of Hull Stress Monitoring Systems.